Steel in Automotive Manufacturing: Innovations, Benefits, and Future Trends
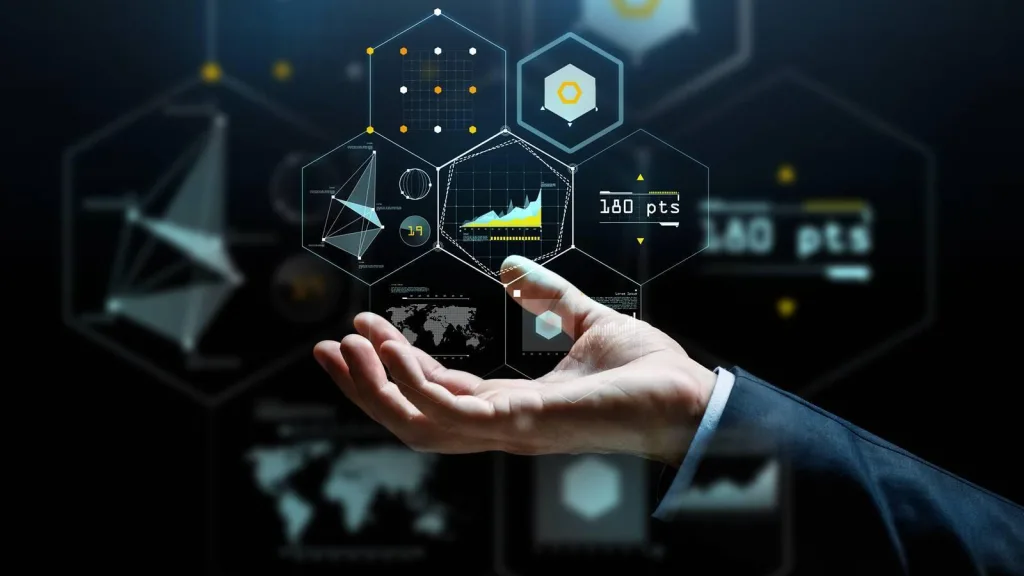
Introduction
Steel has been a fundamental material in automotive manufacturing for over a century. Its unique combination of strength, durability, and cost-effectiveness makes it indispensable for building safe and efficient vehicles. As the automotive industry evolves with new technologies and sustainability goals, steel continues to play a critical role. This article delves into the innovations, benefits, and future trends of steel in automotive manufacturing.
The Role of Steel in Automotive Manufacturing
- Strength and Safety:
- Crashworthiness: Steel’s high tensile strength and energy absorption capabilities make it ideal for manufacturing crash-resistant vehicle structures, ensuring passenger safety.
- Structural Integrity: The use of high-strength steel in the vehicle frame enhances structural integrity, providing a sturdy foundation for modern cars.
- Lightweighting:
- Advanced High-Strength Steel (AHSS): Innovations in AHSS have allowed manufacturers to reduce vehicle weight without compromising safety. Lighter vehicles improve fuel efficiency and reduce emissions.
- Material Optimization: Engineers use a mix of different steel grades in various parts of the vehicle to optimize weight and performance.
- Cost-Effectiveness:
- Production Efficiency: Steel’s versatility and ease of fabrication contribute to cost-effective manufacturing processes. It can be easily stamped, welded, and assembled, making it suitable for mass production.
- Economical Material: Despite competition from alternative materials, steel remains one of the most cost-effective options for automotive manufacturing.
Innovations in Steel for Automotive Manufacturing
- Third-Generation Advanced High-Strength Steel (3G AHSS):
- Enhanced Properties: 3G AHSS offers improved formability and strength, enabling the production of complex shapes and lightweight components.
- Application: These steels are increasingly used in critical areas such as the vehicle’s safety cage, door beams, and bumpers.
- Hot Stamping:
- Strength and Precision: Hot stamping processes involve heating steel blanks before forming them into shape. This technique produces ultra-high-strength steel components with precise geometries.
- Usage: Hot-stamped steel is used in safety-critical components like pillars, roof rails, and side impact beams.
- Coated Steel:
- Corrosion Resistance: Advances in coatings, such as galvanized and aluminized steels, enhance corrosion resistance, extending the lifespan of automotive components.
- Eco-Friendly Coatings: New environmentally friendly coatings reduce the ecological footprint of steel manufacturing.
- Smart Steel Technologies:
- Integrated Sensors: The development of smart steel with integrated sensors helps in real-time monitoring of vehicle performance and structural health.
- Connected Vehicles: Smart steel technologies support the advancement of connected and autonomous vehicles, providing crucial data for safety and maintenance.
Benefits of Steel in Automotive Manufacturing
- Sustainability:
- Recyclability: Steel is one of the most recyclable materials, contributing to a circular economy. Automotive steel can be recycled multiple times without losing its properties.
- Low Carbon Footprint: Modern steel production techniques are becoming more energy-efficient and less carbon-intensive, aligning with global sustainability goals.
- Performance and Comfort:
- Noise, Vibration, and Harshness (NVH): Steel’s damping properties help reduce NVH levels, improving ride comfort and overall vehicle performance.
- Thermal Management: Steel’s thermal properties assist in managing heat within the vehicle, enhancing performance and safety.
- Design Flexibility:
- Aesthetic Freedom: Steel allows for diverse design possibilities, enabling manufacturers to create aesthetically appealing and aerodynamically efficient vehicles.
- Custom Components: Advanced steel processing techniques enable the production of custom components tailored to specific vehicle models.
Future Trends in Steel Automotive Manufacturing
- Sustainable Steel Production:
- Green Steel Initiatives: The push for carbon-neutral steel production methods, such as hydrogen-based steelmaking, is gaining traction. This will further reduce the environmental impact of automotive manufacturing.
- Renewable Energy: Increased use of renewable energy sources in steel production will contribute to the overall sustainability of the automotive industry.
- Integration with Electric Vehicles (EVs):
- Battery Protection: High-strength steel is crucial for protecting EV batteries, ensuring safety in the event of a collision.
- Lightweight Components: Steel’s lightweight properties help offset the weight of EV batteries, improving overall efficiency and range.
- Advanced Manufacturing Techniques:
- 3D Printing: The integration of 3D printing in steel manufacturing allows for the production of complex, high-performance components with reduced material waste.
- AI and Automation: The use of AI and automation in steel production and processing is enhancing precision, reducing costs, and improving product quality.
Conclusion
Steel continues to be an essential material in automotive manufacturing, offering unmatched benefits in terms of strength, safety, cost-effectiveness, and sustainability. As the industry moves towards more sustainable and advanced manufacturing practices, steel’s role will only become more significant. Understanding the innovations and future trends in steel automotive manufacturing is crucial for staying competitive and meeting the evolving demands of the market.