Revolutionizing Industries: Innovations in Steel Alloy Development
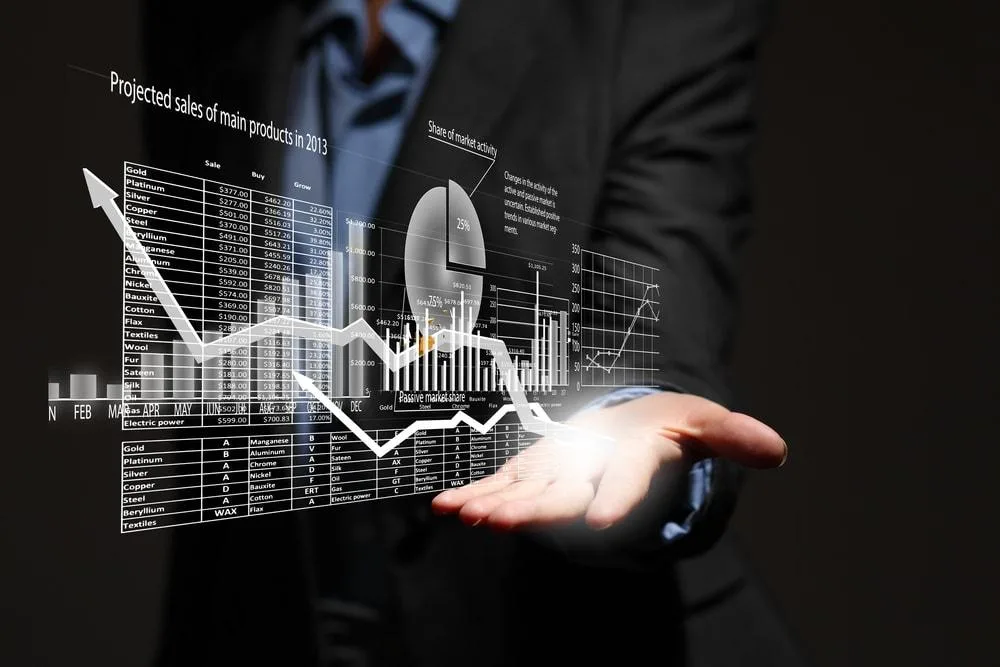
Introduction
Steel alloys have been a cornerstone of industrial development for over a century, offering unparalleled strength, versatility, and durability. Today, innovations in steel alloy development are pushing the boundaries of what is possible, enabling advancements across various sectors, including construction, automotive, aerospace, and renewable energy. This article delves into the latest innovations in steel alloy development, examining cutting-edge technologies, diverse applications, and future trends shaping the industry.
The Evolution of Steel Alloys
- Historical Context:
- Early Innovations: The development of basic steel alloys in the late 19th and early 20th centuries revolutionized construction and manufacturing, laying the foundation for modern industry.
- Technological Advancements: Over the decades, advancements in metallurgy and material science have led to the creation of specialized steel alloys with enhanced properties.
- Modern Innovations:
- High-Strength, Low-Alloy (HSLA) Steels: HSLA steels offer superior mechanical properties and corrosion resistance, making them ideal for demanding applications in construction and automotive industries.
- Advanced High-Strength Steels (AHSS): AHSS, including dual-phase (DP) and transformation-induced plasticity (TRIP) steels, provide exceptional strength and ductility, essential for modern automotive safety and efficiency.
Cutting-Edge Technologies in Steel Alloy Development
- Nano-Alloying:
- Nanostructured Steels: Incorporating nanoscale elements into steel alloys enhances strength, toughness, and wear resistance, opening new possibilities for high-performance applications.
- Applications: Nano-alloyed steels are increasingly used in aerospace components, high-stress machinery, and cutting-edge medical devices.
- Thermo-Mechanical Processing:
- Advanced Heat Treatments: Innovative heat treatment processes, such as quenching and partitioning (Q&P), optimize the microstructure of steel alloys, resulting in improved mechanical properties.
- Industry Impact: These techniques are vital for producing ultra-high-strength steels for automotive and structural applications.
- Additive Manufacturing:
- 3D Printing with Steel Alloys: Additive manufacturing technologies enable the precise fabrication of complex steel alloy components, reducing material waste and enhancing design flexibility.
- Future Prospects: 3D printing with steel alloys is set to revolutionize industries by allowing for customized, lightweight, and high-strength components.
- Cryogenic Processing:
- Enhanced Performance: Cryogenic treatment of steel alloys significantly improves wear resistance, hardness, and dimensional stability, making it essential for high-performance tools and components.
- Applications: This technology is crucial in aerospace, automotive, and heavy machinery sectors where enhanced material performance is critical.
Applications of Innovative Steel Alloys
- Automotive Industry:
- Lightweighting: Advanced steel alloys contribute to vehicle lightweighting, enhancing fuel efficiency and reducing emissions without compromising safety.
- Safety Enhancements: High-strength steel alloys are used in crumple zones and structural reinforcements to improve crashworthiness.
- Aerospace Sector:
- High-Performance Components: Steel alloys with exceptional strength-to-weight ratios are essential for manufacturing critical aerospace components, including landing gear and engine parts.
- Temperature Resistance: Specialized alloys withstand extreme temperatures and stresses, ensuring reliability and safety in aerospace applications.
- Construction and Infrastructure:
- Durable Structures: Advanced steel alloys provide the necessary strength and durability for constructing long-lasting buildings, bridges, and infrastructure.
- Sustainability: Innovative steel alloys contribute to sustainable construction practices by offering recyclability and reduced material usage.
- Energy Sector:
- Renewable Energy: Steel alloys are integral to the development of wind turbines, solar panel mounts, and hydroelectric infrastructure, supporting the growth of renewable energy.
- Oil and Gas: Corrosion-resistant steel alloys ensure the longevity and safety of pipelines, drilling rigs, and offshore platforms.
Future Trends in Steel Alloy Development
- Sustainability and Eco-Friendly Alloys:
- Green Steel Production: The development of eco-friendly steel alloys focuses on reducing carbon emissions and energy consumption during production, aligning with global sustainability goals.
- Recyclable Alloys: Advances in alloy formulation aim to enhance recyclability, supporting the circular economy and reducing environmental impact.
- Smart and Functional Alloys:
- Self-Healing Steels: Research into self-healing steel alloys aims to develop materials that can repair minor damages autonomously, extending the lifespan of components.
- Multifunctional Alloys: Future steel alloys may incorporate additional functionalities, such as magnetic properties or electrical conductivity, expanding their application scope.
- Integration with Digital Technologies:
- Digital Twin Technology: The integration of digital twins in steel alloy development enables real-time monitoring and optimization of material properties, enhancing production efficiency and quality control.
- AI and Machine Learning: Utilizing AI and machine learning in alloy design accelerates the discovery of new materials with tailored properties for specific applications.
Conclusion
Innovations in steel alloy development are driving significant advancements across multiple industries, from automotive and aerospace to construction and renewable energy. The ongoing research and technological advancements in this field promise to deliver even more specialized and high-performance materials in the future. By staying at the forefront of these innovations, industries can achieve greater efficiency, sustainability, and performance in their applications.